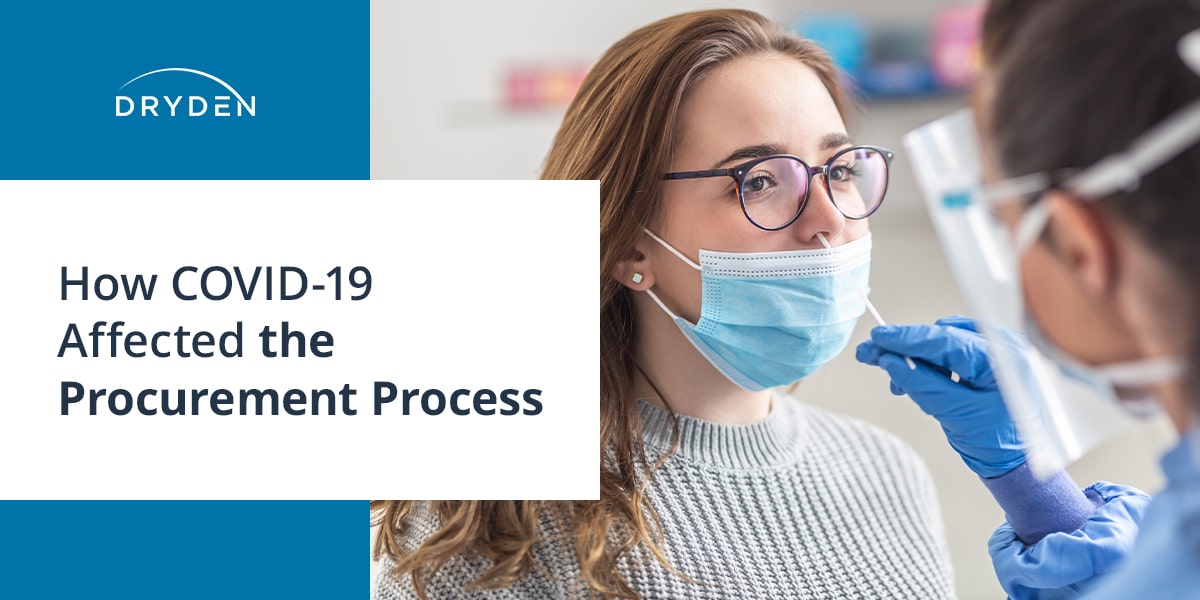
How COVID-19 Affected the Procurement Process Last updated: August 23, 2022
Businesses experienced many changes as a result of COVID-19. Impacts on the supply chain led to companies switching how they approach the procurement process. Understanding how COVID-19 impacted the procurement process can help you develop a stronger, more resilient supply chain for your company.
Procurement Challenges During COVID-19
The emergence of COVID-19 in 2020 caused many product shortages for consumers. The virus strains every supply chain point, from manufacturers and suppliers to distributors and retailers. Many COVID-19-related factors caused these disruptions, including:
- Closed borders: Many distributors and retailers had international suppliers and manufacturers they relied on to stock their goods. When COVID-19 started to spread, many countries closed borders to prevent further spreading and protect their citizens. These actions included prohibiting shipping goods internationally, leaving businesses without a source for their products.
- Increased demand: With stores closed and situations uncertain, demand for items increased drastically and unpredictably. Customers suddenly required more personal protective equipment, like face masks and hand sanitizers. Social distancing and work-from-home arrangements caused people to need more personal items. For example, toilet paper demand rose by 40% in 2020. Manufacturers couldn't keep up with demand, causing more issues further down the supply chain. The increase in delivery demand put additional strain on distributors.
- Limited and restricted labor: State governments and companies instituted social distancing guidelines and employee capacities on locations. While this kept employees safe and healthy, it slowed production and regular operations. Paired with the increased demand, companies faced difficulty keeping up. Even with restrictions, many manufacturers opted to expand operations, functioning at 92% capacity to accommodate customer needs. While this system helped customer satisfaction, it put more strain on companies, employees and equipment to deliver goods.
- Decreased resilience: Many companies across the supply chain did not have the stability needed to maintain operations during the pandemic's start. COVID-19 restrictions and challenges highlighted weak protocols and systems. Without these systems in place, companies had to create mitigating procedures during the middle of the pandemic.
These problems lingered throughout the pandemic while companies struggled to get their stock back to its original levels. Many businesses must revisit their practices and procurement models to create more vital systems that can better function in the face of difficulties.
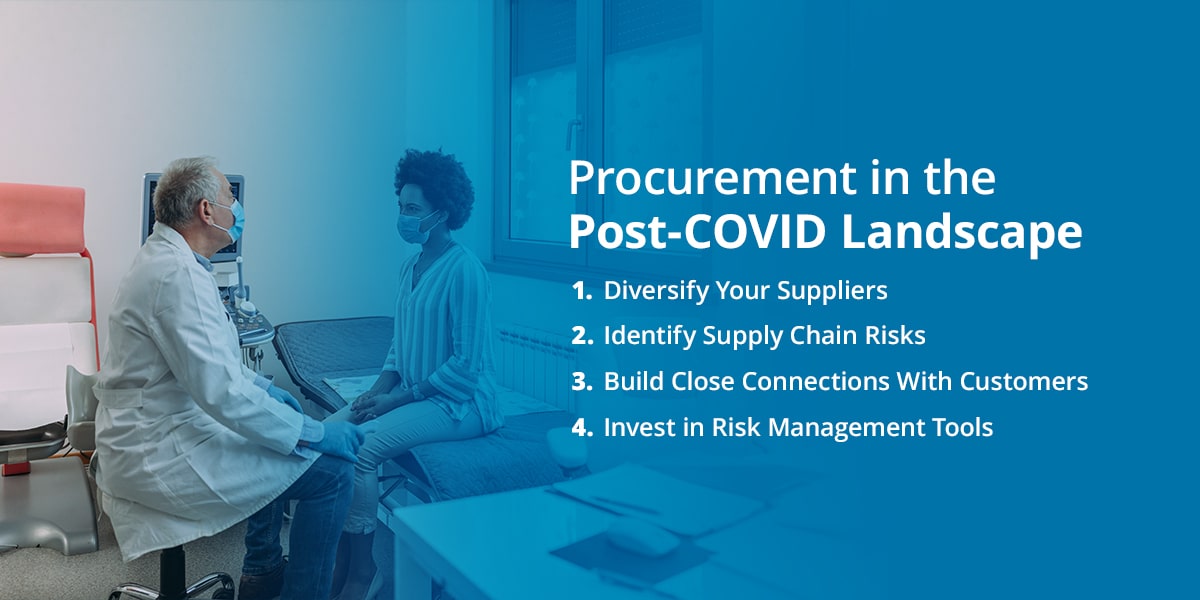
Procurement in the Post-COVID Landscape
While many restrictions have been lifted, businesses still struggle to return to normal. COVID-19 highlighted the need for increased resilience, so companies can better adapt to similar challenges in the future. The pandemic indicated the weak points of the supply chain and now suppliers and distributors can work to strengthen it.
Understanding how to improve your procurement functions can help you build better supply chain management for you and your business partners.
1. Diversify Your Suppliers
Many companies struggled during the pandemic because their suppliers couldn't deliver due to geographic restraints. Closed borders meant businesses with international suppliers suddenly had to explore new procurement methods to find the same goods. With the working restrictions, shipping and manufacturer delays were common and put more strain on local suppliers.
You can decrease your procurement risks by diversifying your supplier partnerships. Expanding to more suppliers reduces the strain on one during difficult times because they can split loads to meet challenges and normal stock levels. When demands suddenly rise for products, you can continue to deliver goods to your customers without overworking your suppliers.
Because COVID-19 highlighted the geographical procurement risks, the impact of a strategic source process has increased. Look at your suppliers' locations. If you have only international suppliers, consider partnering with more domestic and local businesses to reduce the impact international conflicts and issues could have on your supply chain. If you only work with local companies, research some in other locations — if a natural disaster or local problem arises, you can count on your other suppliers to come through.
2. Identify Supply Chain Risks
Knowing the risks posed against your supply chain can better brainstorm tactics to mitigate them. Analyze your supply chain and procurement process for weaker procedures and risks. Do you rely on one transportation type to deliver your goods to your warehouses? Do you get one product from a single supplier? These factors can highlight where you might experience supply chain problems in the future.
You can also use this process to build a stronger relationship with your suppliers. Establish stronger communication and information sharing methods, like digitizing payment processing and invoicing. You can create online information databases that you and your suppliers can use to strengthen decisions and increase your reliability.
Identifying risks and establishing closer relationships with your suppliers can increase the visibility of your supply chains. You can better see problems as they occur and respond quicker. Further, you can work with your suppliers to implement a solution that works for both parties.
3. Build Close Connections With Customers
Your customers can also provide valuable information you can use to drive decisions and strengthen your supply chain. Customers drove many choices at the pandemic's beginning, including the increased demand for toilet paper. When industry standards include overnight shipping and frequent customer updates, working with your customers in a partnership can be a powerful risk reduction tool.
Because supply chain issues have many causes, communication with your customers is pivotal. When you experience struggles or changes, relate them to affected customers. Whether you have delayed shipments that will result in later deliveries or products out of stock, you can keep your customers happy by telling them as you learn information. They can better adjust their lives around changes, reducing the frustration of not knowing.
You can also work with your audience to predict trends and demand changes more accurately. Focus groups, surveys and other communication methods can help you identify items you might need to evaluate for procurement. Customer engagement can help you better analyze demand trends — they can tell you what they want more directly, allowing you to change your procurement process as needed.
Regular customer feedback can provide more information about your customers and their priorities. They might value quick service over updates, influencing you to diversify your suppliers for specific products to stabilize the supply chain.
4. Invest in Risk Management Tools
The tools you have can help you mitigate procurement risks and build a more resilient supply chain. You can invest in new technology that helps monitor stock levels and automatically order more products when they reach a certain threshold. Others monitor supplier communications for better payment reconciliation and efficient shipments.
At Dryden Group, we offer several procurement services to companies across industries. Our consultants understand that every company has unique procurement needs and methods, so we will work with you to create a resilient procurement plan that meets your requirements. Our supplier relationship management services can help you reduce delays, cost spikes and other supplier challenges. We'll help you develop strategies for stronger relationships and partnerships to navigate supplier interactions.
While our industry experience helps us assist companies from all sectors, we offer services for businesses with specific needs, including those who need to procure office supplies or lab equipment.
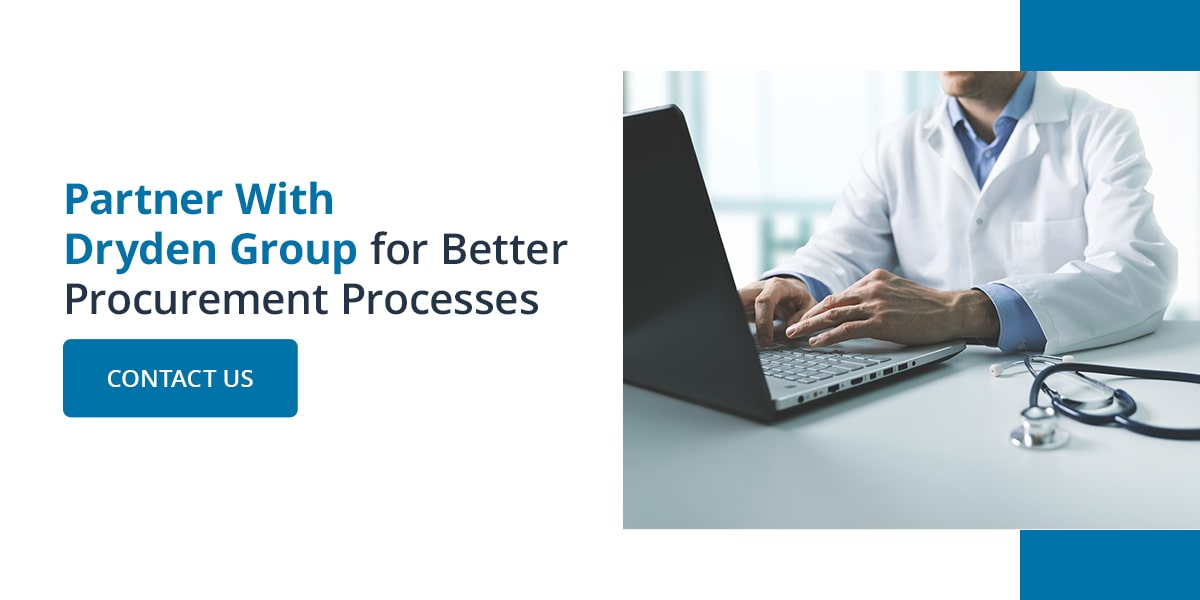
Partner With Dryden Group for Better Procurement Processes
When managing procurement disruptions, having the right tools and services available can help your company navigate challenging times and offer the best services. Supply chain disruptions have many causes, and a team of experienced consultants can ensure you have the strategies and procedures to continue operations.
Contact Dryden Group today and discover how you can build a stronger supply chain response.